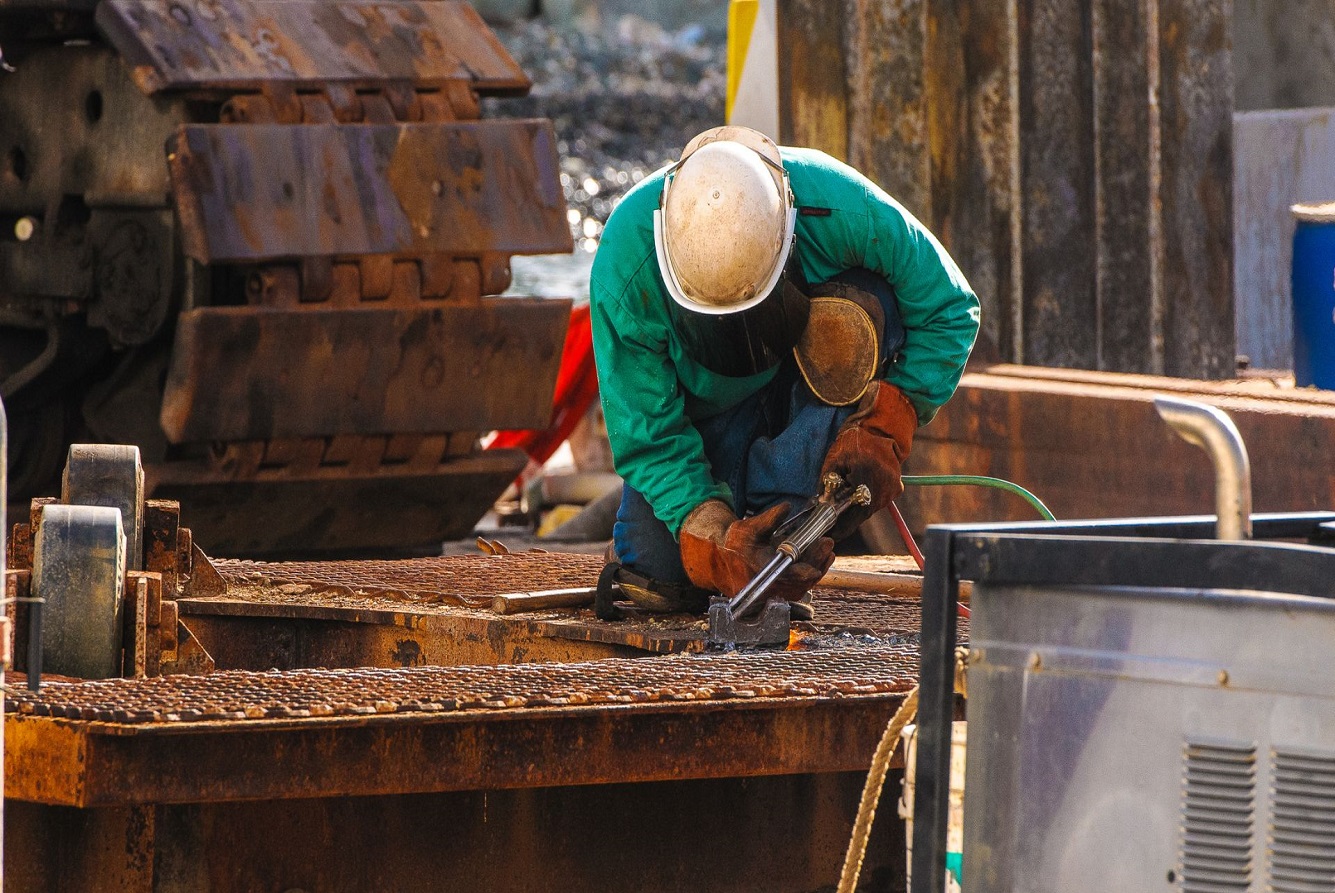
Sheet metal punching is a cutting process that helps in shaping metal forms. Advanced skills and equipment help punch holes in the toughest metal pieces. Most punched holes are geometric shapes like circles, squares, rectangles, etc., but we can also use custom tools to punch complex shapes. Since the punch press can apply a lot of pressure, there are higher chances of making mistakes. That is why it’s important to learn a few basics before trying anything.
How does the Metal Punching Process Work? What Are its Fundamental Principles?
In the process of metal punching, indents and holes are dug in metal sheet using heavy machinery and equipment. The entire process begins with pressing a punch and a die in sheet metal. Then, the punch moves further into the die. It shears away the sheet metal that is attached to the surrounding metal. The cutout piece of metal is then moved to a container for recycling.
As one of the renowned Metal Punching Professionals in Albuquerque, we try to repeat the process until we get the desired result. We also use nibbling as a method to achieve the custom shape. In this process, we make a series of small holes at a time. Then these holes are connected to create customized frames as per the need.
Factors That Affect Punch Quality
- The shape and size of the punch press and die can impact the punch quality.
- The amount of force exerted on the sheet metal is also considered, as it can reach up to 20 tons.
- It’s difficult to punch a thick metal sheet because thicker sheets require more force.
- Harder metal requires greater force to be punched. Pressure is applied after determining the hardness of the metal.
Here are 5 Metal Punching Strategies That can be Used to Fabricate the Best Metal Parts:
- Management of Slugs: While piercing a sheet, the punch creates a hole, and the left-out scrape from this punch is called a slug. It’s during the pulling of this slug that suction forms. It sometimes gets stuck on the face of the punch and slows down the punching process. To reduce lead time, metal punching professionals like New Mexico Metals take measures to break this suction. We cut slots in the punch face to reduce the suctioning effect. The use of a slug retention system also comes in handy for reducing suction. The die needs to be in a negative-positive geometry to properly use this slug retention system. The diameter should be narrower at the top. Then only it will help to retain the slug on the return stroke when the punch comes up. Although it’s effective, the punch must move at a certain distance.
- Galling Prevention: Galling happens when high heat and pressure between the piece and punch make them adhere to each other. We need to ensure that a different grade of material is used between the workpiece and punch. Modern equipment comes with a coating that prevents heat formation during the punching. However, it’s important to use identical tools to get similar results. Die clearance also keeps in check the occurrence of galling. Experimentation with different kinds of material helps in understanding which one is right for die clearance.
- Minimizing Sheet Distortion: The sheet gets distorted if the punch gets into contact with the material. While penetrating and shearing, the punch carries some material inwards. With the help of some changes, this effect can be reduced. The first method is through hole shaving. In this sheet metal punching process, the same kind of die is used in two different punch size diameters. The smaller punch is first used to pierce a hole in the workpiece followed by a larger punch. The second punch thus removes the stressed area surrounding the entire perimeter, leaving behind a clean hole. Clamping pressure is another way to reduce distortion.
- Resolving pinch points: In the process of punching metal, a pinch point can occur when a sheet of metal becomes wedged between the punch and die, causing deformation or equipment damage. The metal suppliers in your area will thus take precautions to stop the formation of pinch points. For instance, altering the design can reduce potential traps for metal sheets. Changes like chamfered edges or rounded corners can help prevent metal from becoming wedged between the punch and die. Similar to design modifications, effective tool selection, operator training, machine guarding, and routine maintenance are some approaches to prevent pinch points from occurring.
- Reducing the Sheet Shake: At New Mexico Metals, we use tools that punch numerous pieces from a single huge sheet that help minimising the sheet shake. Occasionally the metal is not properly fixed in its position. When this happens, the punching operation can move or shake the workpiece, which can lead to sloppy cuts, broken tools, and longer downtime. Your knowledgeable metal service providers will use the proper tools to verify that the punch and die match the material and thickness being punched in order to prevent this from happening. We make sure the metal is well fastened so that it doesn’t move while the operation is underway. Other methods to guarantee the quality of the cut include using a vibration-damping substance, maintaining the machine properly, and lubricating the material being punched.
Metal punching might sound quite easy to you but there are many technical aspects that you need to keep in check while fabricating the best metal piece. It’s best you choose a trusted source like New Mexico Metals LLC to ensure you get quality steel products and services for your next project.
If you want to source high-quality steel products, look no further – Contact Us Today. At New Mexico Metals, we got you covered for all your steel supply needs in Albuquerque.